C2M模式的產(chǎn)業(yè)互聯(lián)網(wǎng)最佳實(shí)踐 服務(wù)器定制化的用戶驅(qū)動創(chuàng)新
C2M是“從消費(fèi)者到生產(chǎn)者”(Customer to Manufacturer)的簡稱,其基于互聯(lián)網(wǎng)、大數(shù)據(jù)、人工智能,以及通過生產(chǎn)線的自動化、定制化、節(jié)能化、柔性化,運(yùn)用龐大的計(jì)算機(jī)系統(tǒng)隨時(shí)進(jìn)行數(shù)據(jù)交換,按照客戶的產(chǎn)品訂單要求,設(shè)定供應(yīng)商和生產(chǎn)工序,最終生產(chǎn)出個(gè)性化產(chǎn)品的工業(yè)化定制模式。這也被稱為繼蒸汽機(jī)、電氣化、自動化之后人類的第四次科技革命。
如今C2M模式在消費(fèi)互聯(lián)網(wǎng)市場已經(jīng)日漸成熟,比如現(xiàn)在電商市場已經(jīng)在大規(guī)模實(shí)踐C2M。其實(shí)除了在2C互聯(lián)網(wǎng)市場,C2M在產(chǎn)業(yè)互聯(lián)網(wǎng)中也有著廣泛的應(yīng)用空間,例如浪潮、曙光、寧暢等服務(wù)器廠商在服務(wù)器定制化領(lǐng)域積極探索由用戶驅(qū)動生產(chǎn)的反向生產(chǎn)模式。
用戶需求驅(qū)動的服務(wù)器定制化市場
定制化是生產(chǎn)力發(fā)展的必然產(chǎn)物。在生產(chǎn)力發(fā)展的初級階段,標(biāo)準(zhǔn)化、統(tǒng)一化的產(chǎn)品能夠快速打開市場,滿足絕大多數(shù)的用戶需求;但是隨著生產(chǎn)力的發(fā)展,許多用戶已經(jīng)不滿足于標(biāo)準(zhǔn)化產(chǎn)品帶來的固定服務(wù),他們千差萬別的需求為定制化的出現(xiàn)提供了空間,也成為了定制化發(fā)展的最強(qiáng)推動力。
經(jīng)過了20多年發(fā)展之后,放諸四海而皆準(zhǔn)的產(chǎn)品方案已經(jīng)與時(shí)代脫節(jié),中國服務(wù)器市場已經(jīng)進(jìn)入到精細(xì)化定制階段。其實(shí)不僅僅是服務(wù)器,整個(gè)時(shí)代都在呼喚定制化的產(chǎn)品和服務(wù)。
面對“新基建”大潮,具有“智能運(yùn)維”、“快速部署”、“高效性能”、“可批量交付”特征的服務(wù)器已成行業(yè)剛需。而傳統(tǒng)通用服務(wù)器ODM、OEM管理體系已不能滿足“新基建”背景下的產(chǎn)業(yè)發(fā)展需求。
比如服務(wù)器市場,伴隨著云計(jì)算、5G、人工智能等技術(shù)的發(fā)展,服務(wù)器的形態(tài)和用途也發(fā)生了改變,不同的工作負(fù)載對服務(wù)器能力產(chǎn)生了不同的需求。就要求服務(wù)器廠商能夠提供適應(yīng)不同用戶使用的、差異化的解決方案。
特別是全球數(shù)據(jù)中心市場規(guī);⒓s化、綠色化趨勢,定制化服務(wù)器的需求日趨強(qiáng)烈,其中以BAT為代表的對數(shù)據(jù)中心需求巨大的大型互聯(lián)網(wǎng)公司中尤為常見。服務(wù)器的定制可以說是一種全新的應(yīng)用模式,根據(jù)用戶的不同需求,定制出符合業(yè)務(wù)需求的定制化產(chǎn)品,可以使得服務(wù)器的性能與業(yè)務(wù)的需求契合度更高。
如果從這樣的定義,我們看到服務(wù)器定制化其實(shí)就是一種C2M模式。定制的本質(zhì)是根據(jù)客戶需求量體裁衣,“按需配置”是定制化服務(wù)器最為顯著的特點(diǎn),差異化的需求造就了差異化的產(chǎn)品,同時(shí)也就有了成百上千種的定制化需求。
服務(wù)器的定制化需求對于服務(wù)器廠商的生產(chǎn)能力提出了更高的要求,如何更好地滿足客戶以及快速交付成為當(dāng)前服務(wù)器廠商的重要課題。服務(wù)器生產(chǎn)離不開工廠建設(shè)的支持,為了更好地支撐服務(wù)器定制化生產(chǎn),我們看到眾多服務(wù)器廠商進(jìn)行廣泛的布局。
JDM模式驅(qū)動的智能工廠實(shí)踐
浪潮位于濟(jì)南的智能工廠,是中國第一個(gè)服務(wù)器智能柔性生產(chǎn)基地,中國服務(wù)器領(lǐng)域第一條高端裝備智能生產(chǎn)線,被評為全球智能制造典范的智能工廠,實(shí)現(xiàn)了人工智能、工業(yè)互聯(lián)網(wǎng)與制造業(yè)的緊密結(jié)合。該工廠采用了大量自動化設(shè)備,包括AGV、機(jī)械手、機(jī)械臂、自動化檢測設(shè)備等,配備了2條柔性智能產(chǎn)線、1座智能立體倉庫、8座智能老化中心和實(shí)驗(yàn)室,以及一座智能現(xiàn)代化的物流中心,通過集成600多個(gè)RFID、2000多個(gè)傳感器、50個(gè)設(shè)備控制器、330套智能設(shè)備、6大核心系統(tǒng),依托CRM、ERP、MES等軟件系統(tǒng)實(shí)現(xiàn)了從柔性化生產(chǎn)到交付服務(wù)的全過程智能化。
依托于敏捷創(chuàng)新的JDM模式,浪潮打通互聯(lián)網(wǎng)、能源、通信等客戶需求,快速聯(lián)合研發(fā)了AI邊緣盒子、NE5260M5、整機(jī)柜SR等一系列定制化產(chǎn)品。同時(shí)JDM基于敏捷高效的交付,能夠快速滿足客戶突然爆發(fā)增長的新場景如雙十一、春晚紅包。
在浪潮的智能工廠,車間內(nèi)來回穿梭的智能AGV小車,運(yùn)輸全程自動化、物料全程不落地的生產(chǎn)現(xiàn)場,不停揮舞著機(jī)械手全自動精準(zhǔn)作業(yè)的智能化機(jī)器人,物料自動識別且自動出庫的智能立體倉庫……正前方屏幕上顯示的是工廠的生產(chǎn)管理看板,上面有百度、阿里的大訂單,也有中小客戶的小訂單。”客戶“一鍵下單”,客戶定制化的需求通過系統(tǒng)自動轉(zhuǎn)化成生產(chǎn)裝配的“作業(yè)指導(dǎo)”和“工藝要求”,直接呈現(xiàn)在工人面前。這些訂單在一條線上并行執(zhí)行,任務(wù)分配有條不紊,充分體現(xiàn)了互聯(lián)網(wǎng)+的思路和訂單即制造的柔性生產(chǎn)特點(diǎn)。
浪潮集團(tuán)副總裁孔亮介紹說,客戶通過CRM下單,信息進(jìn)入ERP系統(tǒng),ERP自動進(jìn)行物料計(jì)算,生成生產(chǎn)任務(wù),接下來進(jìn)入MES系統(tǒng),MES會統(tǒng)籌整個(gè)生產(chǎn)過程的調(diào)度運(yùn)行。產(chǎn)品裝備完成后,進(jìn)入高溫壓測中心,進(jìn)行48小時(shí)或者更久的高溫、高壓等可靠性測試,最后通過TMS物流管理系統(tǒng),完成全球范圍內(nèi)的發(fā)貨和交付。“貫穿整個(gè)生產(chǎn)環(huán)節(jié)的,不僅僅是工廠制造數(shù)據(jù)管理、計(jì)劃排程管理、生產(chǎn)調(diào)度管理、庫存管理、質(zhì)量管理等全流程自動化控制,更為重要的是實(shí)現(xiàn)全流程的數(shù)據(jù)采集和分析,通過數(shù)字化、智能化的手段驅(qū)動需求、研發(fā)、生產(chǎn)、服務(wù)4端之間的互聯(lián)協(xié)同。”
效率的提高帶來了浪潮服務(wù)器整體交付能力的提高,浪潮智能工廠的整體交付周期從18天縮短至5-7天,生產(chǎn)效率提升30%,客戶TCO降低31%。得益于如此顯著的成效,浪潮智能工廠成功入選2017年國家智能制造試點(diǎn)示范,并被Gartner評為全球智能制造典范。
浪潮智能工廠采用自動化、智能化技術(shù),也采用了5G的很多技術(shù),實(shí)現(xiàn)了高效的智能制造。孔亮表示,整個(gè)行業(yè)越來越嚴(yán)格的成本控制、交付效率和質(zhì)量訴求,都要求制造業(yè)必須走向智能化和自動化,這無疑是中國制造的大方向。
2分鐘組裝一臺服務(wù)器
其實(shí)除了浪潮,曙光在之智能工廠方面也邁出了堅(jiān)實(shí)的步伐。在生產(chǎn)線上2分鐘組裝一臺服務(wù)器,按現(xiàn)在的制造水平幾乎是不可能完成的任務(wù),但在曙光(福建)智能工廠實(shí)現(xiàn)了,這“2分鐘”是曙光全廠智能制造能力的綜合呈現(xiàn)。對于服務(wù)器這樣的產(chǎn)品設(shè)計(jì)制造,它應(yīng)該滿足“智能綠色,精益融合”的理念,而這一理念,同樣成為曙光打造智能工廠的核心理念。
曙光通過對智能制造進(jìn)行系統(tǒng)設(shè)計(jì),建立工藝生產(chǎn)流程與車間虛擬仿真模型,結(jié)合5G、人工智能、數(shù)字孿生等技術(shù)在智能制造中應(yīng)用的能力,打造了ERP、MES及工業(yè)大數(shù)據(jù)平臺等企業(yè)信息化平臺,建立起曙光智能工廠的工業(yè)大腦,打造出了“曙光式”的智能制造工廠模板。
曙光智能制造工廠擁有智能內(nèi)存檢測設(shè)備、智能硬盤裝配設(shè)備等一大批核心裝備,支撐智能工廠的自動化。而智慧倉儲物流顯著提升了訂單生產(chǎn)與交付效率。包括自動化包裝、物料管理、前加工、整機(jī)裝配、老化測試、動力系統(tǒng)、定制工單等。
圍繞核心智能裝備、智慧倉儲物流、數(shù)字孿生模型、信息互聯(lián)互通、工業(yè)大數(shù)據(jù)平臺等核心要素,曙光構(gòu)建完備的智能制造系統(tǒng)解決方案,更好地滿足服務(wù)器生產(chǎn)的需求。
在曙光(福建)高端服務(wù)器智能工廠獲得了單位產(chǎn)值能耗降低20%、運(yùn)營成本降低20%、產(chǎn)品升級周期縮短30%、生產(chǎn)效率提升35%,實(shí)現(xiàn)了2分鐘組裝出一臺服務(wù)器。目前,曙光高端整機(jī)智能制造工廠在新疆、福建、山西、江蘇等已經(jīng)落地并投產(chǎn)。
中科曙光副總裁張迎華表示,在工業(yè)4.0定制化時(shí)代,先進(jìn)計(jì)算力就是生產(chǎn)力。先進(jìn)計(jì)算與智能制造融合發(fā)展成為必然。目前,曙光智能工廠大量使用先進(jìn)計(jì)算技術(shù),來支持曙光先進(jìn)計(jì)算設(shè)備的定制化創(chuàng)新與生產(chǎn)。
當(dāng)前,以智能工廠、C2M定制化生產(chǎn)等為代表的一批制造業(yè)新形態(tài),正成為傳統(tǒng)制造業(yè)化解不確定性風(fēng)險(xiǎn)的重要工具。2007年起,曙光就已建立定制化產(chǎn)品團(tuán)隊(duì),開始涉足服務(wù)器定制化業(yè)務(wù),是國內(nèi)最早的服務(wù)器定制化供應(yīng)商。深耕定制化領(lǐng)域12載,曙光從客戶需求的調(diào)查到產(chǎn)品研發(fā)、生產(chǎn)、供貨、服務(wù)等等,建立了一套完整的供應(yīng)體系。
特別是曙光設(shè)立了一支具備快速研發(fā)與快速定制產(chǎn)品能力的團(tuán)隊(duì),與客戶的研發(fā)團(tuán)隊(duì)進(jìn)行直接對接,高效溝通、密切協(xié)作,極大地簡化了交付、部署等工作,提高交付效率10倍以上。
開啟服務(wù)普惠定制時(shí)代
雖然大型互聯(lián)網(wǎng)廠商對于服務(wù)器定制化需求強(qiáng)烈,但是我們不能忽視中小型企業(yè)的服務(wù)器定制需求,畢竟在數(shù)字經(jīng)濟(jì)蓬勃發(fā)展的今天,用戶的多樣化需求得到了極大釋放。
寧暢副總裁及首席技術(shù)官趙雷告訴記者,對于中小型企業(yè),定制化服務(wù)器需求雖然沒有大企業(yè)高但依然存在,且相對來講他們的定制滿足度比傳統(tǒng)的大型企業(yè)差,這也是類似寧暢專注定制化服務(wù)器生產(chǎn)廠商的機(jī)遇。
為滿足市場對定制化服務(wù)器產(chǎn)品需求,寧暢正開啟服務(wù)普惠定制時(shí)代,將定制化服務(wù)器的行業(yè)數(shù)量門檻從目前的超10萬臺降到1萬臺及以下。這可讓過去沒資源享受定制便捷化的客戶,也享受服務(wù)器定制化服務(wù)。
服務(wù)器定制化需要很高技術(shù)門檻,具有以定制化方式實(shí)施各種數(shù)據(jù)中心項(xiàng)目的公司并不多。以寧暢來說需要三大技術(shù)平臺,20余項(xiàng)核心技術(shù)的支持,才可真正實(shí)現(xiàn)服務(wù)器產(chǎn)品按需定制化,并結(jié)合智能制造模式,才可完成產(chǎn)品的更迭。
寧暢在行業(yè)內(nèi)創(chuàng)新性地構(gòu)建出“精細(xì)定制產(chǎn)品開發(fā)體系”,可實(shí)現(xiàn)服務(wù)器產(chǎn)品的按需、精細(xì)化開發(fā),滿足數(shù)據(jù)中心、IT、以及電信等行業(yè)用戶,對服務(wù)器架構(gòu)、運(yùn)維、軟件、硬件等多個(gè)維度進(jìn)行定制的需求。
在具體定制服務(wù)器產(chǎn)品開發(fā)中,為保證產(chǎn)品交付質(zhì)量與速度。有別與傳統(tǒng)ODM、OEM所說的管理體系,寧暢以CDSPD研發(fā)平臺為基礎(chǔ),快速落地定制產(chǎn)品。該平臺研發(fā)流程通俗分為四個(gè)階段。第一階段,需求階段。主要是分析用戶痛點(diǎn)、落地產(chǎn)品需求,設(shè)置開發(fā)流程。第二階段,架構(gòu)設(shè)計(jì)階段。定制化服務(wù)器架構(gòu)設(shè)計(jì)階段要求比傳統(tǒng)、標(biāo)準(zhǔn)服務(wù)器高很多,因此架構(gòu)設(shè)計(jì)決定了最終產(chǎn)品對用戶痛點(diǎn)、核心訴求的支撐,并滿足要高效、節(jié)約成本,并可快速交付。第三階段,迭代開發(fā)測試階段。跟傳統(tǒng)模式比較,寧暢定制產(chǎn)品迭代測試最快是一晚,最慢3-4晚完成。第四階段,維護(hù)與服務(wù)階段。包括升級、協(xié)助運(yùn)維服務(wù)等。
測試在定制服務(wù)器生產(chǎn)中是非常重要的環(huán)節(jié),寧暢公司具有500臺機(jī)群測試能力,質(zhì)量測試模型超過5000項(xiàng),自動化測試率達(dá)99.8%。只有通過自動化測試技術(shù),才能降低對人力的需求,以維持公司業(yè)務(wù)快速增長。此外,自動化測試還包括100%在線數(shù)據(jù)分析系統(tǒng),包括BMC、智能網(wǎng)卡等測試數(shù)據(jù),通過寧暢在線數(shù)據(jù)分析收集系統(tǒng)集中,再配合大數(shù)據(jù)分析系統(tǒng),可自動定位問題點(diǎn)并給出初步分析。這樣的話在維護(hù)階段只需3天便可完成軟件升級版本的迭代驗(yàn)證。
本文章選自《數(shù)字化轉(zhuǎn)型方略》雜志,閱讀更多雜志內(nèi)容,請掃描下方二維碼
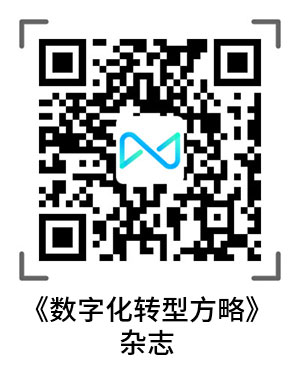